Phosphate ore, as an important chemical mineral raw material, can be used in important industrial sectors such as medicine, food, ceramics, and national defense. In the mineral processing plant, choosing the appropriate phosphate mineral extraction process is one of the main ways to improve the utilization rate of minerals. The following six phosphate ore mineral extraction processes will be introduced to you.
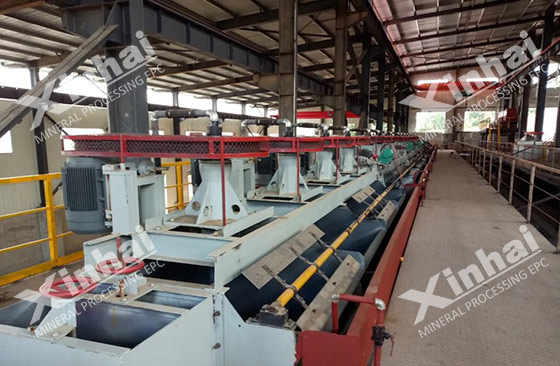
Use the table of contents below to navigate through the guide:
01Phosphate ore direct positive flotation technology
The direct positive flotation technology first suppresses gangue minerals through inhibitors, and then uses collectors to collect phosphorus minerals. During flotation, the temperature of the slurry needs to be kept at 35-40°C, and the proportion of -74μm minerals is required to be more than 90%. This process can be applied to siliceous or calcium-siliceous phosphate ore, endogenous apatite, and sedimentary phosphate ore, and the effect of this process on sedimentary phosphate ore is more obvious.
02Single reverse flotation technology for phosphate ore
The reverse flotation method is mainly used to process phosphate ore with dolomite as the main gangue mineral. The main process is to use the inhibitor sodium phosphate to inhibit the flotation of phosphorus minerals under weakly acidic conditions (pH=4-5), and then use specific collectors (oleic acid and kerosene) to float dolomite. The removal rate of dolomite in the process can reach 70-80%. The single flotation process of phosphate ore does not require heating and can be carried out at low temperature or normal temperature, so the concentrator can reduce energy consumption and save costs, but this process has poor separation effect on calcareous phosphate ore and siliceous phosphate ore. It can be widely used in dense massive or striped phosphorus minerals.
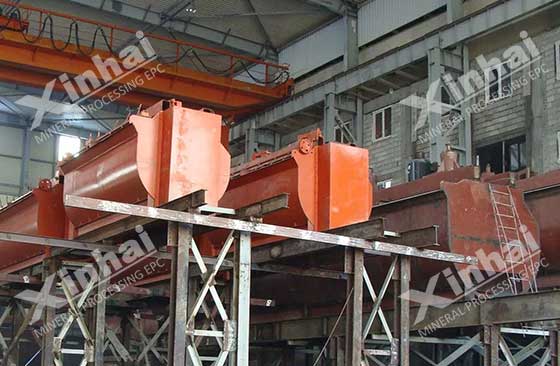
03Phosphate ore positive-reverse flotation technology
This forward-reverse flotation can be used to treat calcium-silicious phosphate ore or silico-calcareous phosphate ore. The flow of this process is: in the positive flotation stage, the pH of the pulp is adjusted to weak alkaline, which can inhibit silicate minerals. The collector is added to the pulp to enrich useful phosphorus minerals and some carbonate minerals in the foam product, and the minerals left in the tank are discharged as gangue minerals. The reverse flotation stage is to adjust the pH of the foam product to weak acidity, and then use a specific collector to enrich impurities such as carbonates, and the minerals left in the tank are concentrates. The concentrate grade obtained by direct-reverse flotation is higher than that of single direct/reverse flotation, and the reverse flotation stage does not require heating, so it has a wider range of applications.
04Reverse-positive flotation technology of phosphate ore
This process is opposite to the above-mentioned forward-reverse flotation process. It uses H2SO4 or H3PO4 to suppress the phosphorus mineral pulp until the pulp is acidic, and then uses the corresponding collector to enrich the carbonate minerals in the foam product and float them out. , the minerals left in the tank are phosphate ore concentrates, and the positive flotation stage is carried out under alkaline conditions, and the silicate minerals in the products in the tank are first suppressed, and the foam product is phosphate ore concentrates. Since the hardness of siliceous minerals in phosphate ore is greater than that of phosphate ore minerals, and the hardness of carbonate minerals is lower than that of the former two, it is necessary to set up a grinding process during positive flotation to increase the degree of mineral dissociation and the reaction between drugs and target minerals. time. This technological process has the advantages of energy saving and consumption reduction.
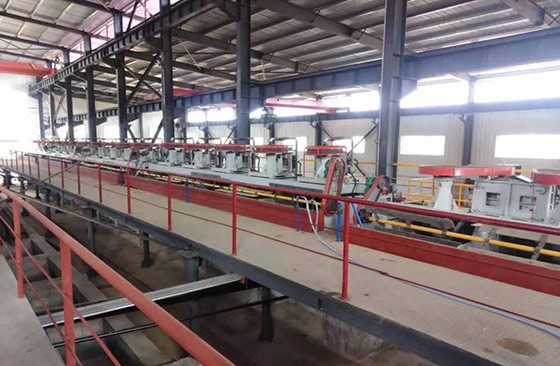
05Phosphate ore double reverse flotation technology
Phosphate ore double reverse flotation technology can be used to process siliceous gangue minerals and mixed phosphorites with low carbonate content, especially the separation effect on dolomite and quartz-like gangue minerals is more obvious. When the process is in progress, use inorganic acid as the main pH regulator, use fatty acid collectors to float out a part of dolomite gangue minerals, and then use fatty amine collectors to collect suitable minerals, and the minerals left in the tank For phosphate ore concentrate. This technological process can be used in a wide range of particle sizes, and it also has a better flotation index for coarser-grained minerals. This process can realize flotation at low temperature or normal temperature, the process is simple, and the reagents required are relatively small.
06Phosphate ore gravity (magnetic)-flotation combined technology
There are many types of phosphate ores. For phosphate ores with special properties, it is sometimes necessary to adopt a combined gravity separation-flotation process, a combined magnetic separation-flotation process or a combined gravity separation-magnetic separation-flotation process. The characteristics of the selected ore itself can be utilized to a greater extent by adopting the joint beneficiation process. Gravity separation can be used to pre-recover dense minerals or pre-throwing tails, and magnetic separation can be used to remove magnetic minerals. Both gravitational separation and magnetic separation are physical separations without adding chemicals, which can reduce the consumption of chemicals and the cost of beneficiation, and reduce the pollution of wastewater to the environment.
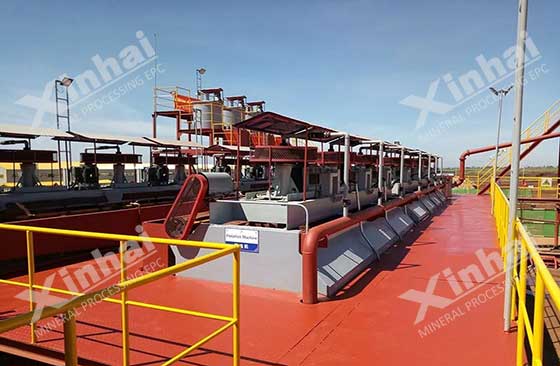
The above are the six technologies for phosphate ore mineral extraction process. Because of the different types of phosphate ore, the beneficiation technology that needs to be adopted is also different accordingly. It is necessary to choose the appropriate beneficiation method according to the nature of phosphate ore. Therefore, Xinhai Mining recommends that before beneficiation conduct beneficiation tests to customize efficient phosphate ore beneficiation technology.