Potassic feldspar is widely used in the glass and ceramic industries. Due to the rapid growth of the market demand for potassic feldspar, especially high-quality ore in recent years, it is imperative to rationally develop and utilize medium and low-grade potassic feldspar resources. In the beneficiation process of potassic feldspar, iron removal and quartz separation are the main problems. The following mainly focuses on three methods for removing iron from potassic feldspar.

Use the table of contents below to navigate through the guide:
01Potassic feldspar washing and iron removal method
To process feldspar from weathered granite or feldspar placer, concentrators can use ore washing to remove iron. This method is mainly used to remove iron-containing impurities such as clay, fine mud and mica. When potassium feldspar is washed, the concentrator can use vibrating screen or washing tank, because clay, fine mud, mica and other iron-containing impurities have small particle size and slow settling speed, so it is easy to separate from coarse-grained feldspar under the action of water flow. The ore washing and iron removal method can reduce the content of ferric oxide in the potassium feldspar, and can also relatively increase the content of potassium and sodium in the ore. This method has been widely used in a variety of feldspar impurity removal processes.

02Potassic feldspar magnetic separation iron removal method
The potassium feldspar magnetic separation iron removal method uses the magnetic properties of impurities such as iron minerals, mica and garnet in the ore to separate the iron-containing impurities from the potassium feldspar under the action of an external magnetic field. However, the magnetic properties of these iron-containing impurities are weak, so in order to achieve a good separation effect, the concentrator needs to use strong magnetic separation equipment.

Different types of strong magnetic separators can also be used to process different kinds of feldspar. For example, pulsating high gradient magnetic separation equipment can be used to treat weathered pegmatite monzonite porphyry ores. It can remove weak magnetic iron-containing impurities such as mica and amphibole, the iron removal rate can exceed 84%, and the feldspar recovery rate can reach about 85%. The permanent magnet roller type strong magnetic separator is used to treat the feldspar ore with a particle size of less than 120 mesh and an iron content of 0.5%-0.8%. After using this equipment, the content can be reduced to 0.15%-0.3%, and the iron removal effect is obvious. . Wet flat ring high magnetic separator is a widely used electromagnetic high magnetic separation equipment in beneficiation plants at home and abroad. Feldspar raw ore with iron content of about 0.5% can be reduced to less than 0.2% after one magnetic separation of this equipment. This equipment also has the advantages of wide selected particle size and large equipment processing capacity. From this, it can be known that the concentrator should choose the appropriate magnetic separation equipment according to the characteristics of the ore itself.

03Potassic feldspar combined process iron removal method
Due to the different characteristics of feldspar, a single technical means sometimes cannot remove iron-containing impurities in feldspar ore well, so the concentrator needs to adopt a combined process to remove iron from potassium feldspar.
1. Flotation + sulfuric acid leaching method
When the iron oxides in the potassium feldspar ore closely coexist with the feldspar minerals, some iron oxides will form a glass melt with the minerals during the mineralization process of the potassium feldspar, which makes the iron removal process more difficult. When processing this ore, the concentrator can use the flotation-sulfuric acid leaching method. This method can reduce the content of ferric oxide in the ore to about 0.11%. This method has the advantages of simple operation and small investment. In addition, the sulfuric acid leaching solution can be recycled.
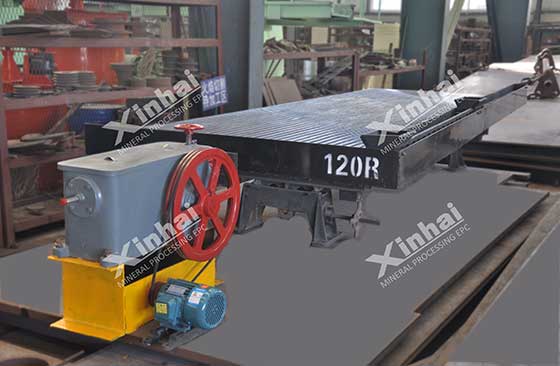
2. Gravity separation + magnetic separation + alkaline washing method
The main process of this method is as follows: after potassium feldspar gravity separation and magnetic separation, iron activator and leaching agent are added to separate potassium feldspar and iron-containing impurities under alkaline conditions. This method can reduce the content of ferric oxide in potassium feldspar to the range of 0.1%-0.2%, and the color of potassium feldspar can be changed from light red to natural color, becoming high-quality potassium feldspar. This method mainly uses chemical methods to separate iron impurities in feldspar. The technological process is advanced, the equipment is simple, the investment is small, and the effect is quick. The alkaline washing liquid and iron-containing wastewater after impurity removal can be recycled after purification treatment.

3. Magnetic separation + flotation method
When dealing with high iron potassium feldspar, compared with the iron removal effect of magnetic separation, flotation and their combined process, the combined process of magnetic separation + flotation has a better iron removal effect. Using magnetic separation + flotation to remove iron from potassium feldspar, the iron removal rate of about 95% can be obtained.

4. Reverse flotation + strong magnetic separation
The main process of reverse flotation + strong magnetic separation method is: first use a mixed collector containing anions and cations to reverse flotation of fine-grained iron-containing substances, and then use the strong magnetic separation process to remove coarse-grained iron minerals And biotite, you can get high-quality potassium feldspar concentrate.
The above are the three methods of removing iron from potassium feldspar. The beneficiation plant should formulate the appropriate beneficiation process according to the results of the beneficiation test. Xinhai can provide you with customized potassium feldspar beneficiation plan and a complete set of beneficiation equipment. If necessary, welcome to consult Xinhai Mining.