Flotation is one of the common methods of iron ore beneficiation, which is mainly used to process iron minerals with fine grains disseminated and difficult to be separated. According to its chemical composition, iron ore is mainly divided into hematite, magnetite, limonite, siderite, ilmenite, and so on, and all can be separated by flotation. In the following, we will introduce five iron ore flotation methods.
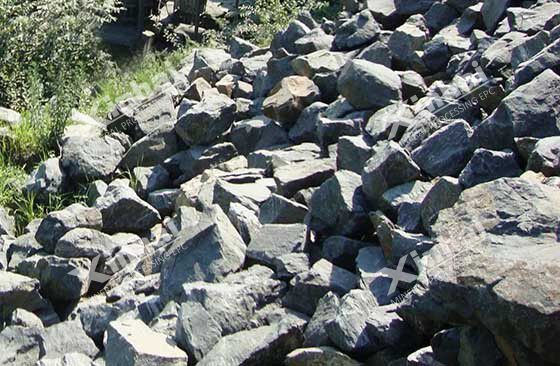
Use the table of contents below to navigate through the guide:
01Hematite Flotation Process
The main methods of hematite flotation are positive flotation, reverse flotation, positive -reverse flotation, and combined flotation.
1. Positive Flotation
Positive flotation mainly uses anionic collectors to float iron ore from raw ore and can discard tailings without desliming under coarse-grained conditions, which is suitable for processing single iron ore.
2. Reverse Flotation
Reverse flotation uses anionic or cationic collectors to float gangue minerals from raw ore, mostly suitable for processing iron ore with high grade and easy-to-float gangue.
3. Positive - Reverse Flotation
Positive - reverse flotation is to carry out the positive flotation first, scrape the iron ore concentrate foam and then transport it to another flotation machine for reverse flotation, and finally the iron ore concentrate is enriched in the flotation cell of the reverse flotation.
4. Combined Flotation
There are two main types of combined flotation: magnetic separation - reverse flotation and strong magnetic separation - flotation. Among them, the magnetic separation-reverse flotation method is to separate the iron ore by magnetic separation first. The remaining minerals are reverse flotation in neutral pulp (pH 7) using dodecylamine cations as collectors. Strong magnetic separation - flotation is a method of separating gangue minerals such as coarse monomer quartz and chlorite which is easy to be muddied by high-intensity magnetic separation, and then fine grinding and flotation.
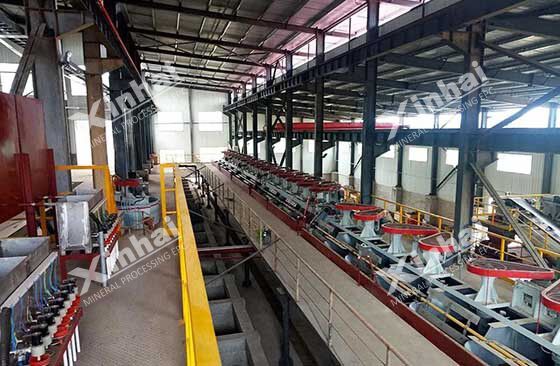
02Magnetite Flotation Process
When processing magnetite, flotation is generally not used alone and is often combined with magnetic separation, which is a weak magnetic separation-flotation combined process. That is to recover iron by the low magnetic separation process, and then recover sulfide or apatite through a flotation process.
Limonite Flotation Process
Limonite flotation mainly includes positive flotation, reverse flotation, and selective flocculation flotation.
1. Positive Flotation
Normally, positive flotation is not used alone but combined with a strong magnetic separation process.
2. Reverse Flotation
Reverse flotation can perform single flotation through the combination of anions and cations. It is mainly suitable for the quality improvement and impurity reduction of iron ores with relatively simple ore properties.
3. Selective Flocculation Flotation
After fine grinding, sodium carbonate and sodium silicate are added to disperse the pulp. Use selective flocculation to selectively flocculate limonite, and then use flotation to obtain high-grade limonite concentrate.
The recovery effect of fine limonite by positive and reverse flotation is better. However, the flotation effect will be seriously affected because the ore easily slimes. Therefore, desliming or strengthening dispersed slime can be considered before flotation.
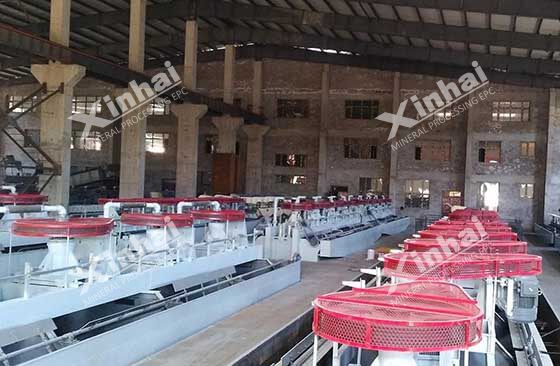
03Siderite Flotation Process
Both positive flotation and reverse flotation methods can be used for siderite flotation both of which are suitable for processing mixed siderite.
Positive Flotation
After siderite is deslimed, the iron minerals are flotation by adding fatty acid collector in neutral or weak acidic medium. In addition, it is not necessary to de-slime after grinding. In addition, it is not necessary to desliming after grinding. Soda and other regulators can be added to the weak alkaline medium, and oxidized paraffin soap and tar oil can be used as collectors for flotation.
Reverse Flotation
The siderite reverse flotation process mainly includes anionic collector reverse flotation and cationic collector reverse flotation. Anionic collector reverses the flotation process is to adding calcium salt to activate quartz in a strongly alkaline medium, mixing sodium hydroxide or sodium hydroxide with sodium carbonate, adjusting the pH value to more than 11, using starch or lignin sulfonate as iron ore inhibitor, use fatty acid as collector, to flotation quartz and other silicates. Cationic collector reverses flotation process is to adjust the pH value of sodium carbonate to 8-9, inhibits siderite material by starch, dextrin, tannin, and other substances, and flotation quartz gangue by amine collector.
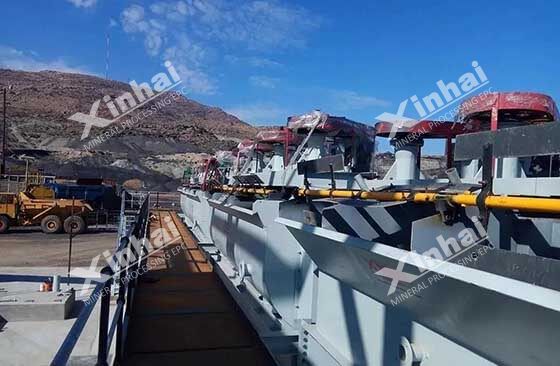
04Ilmenite Flotation Process
The commonly used flotation methods of ilmenite are mainly conventional flotation, flocculation flotation, and agglomeration flotation.
Conventional Flotation
Conventional flotation mainly uses oleic acid and its soap, oxidized paraffin soap, tar oil, and other reagents to separate ilmenite by collecting and flotation.
Flocculation Flotation
Ilmenite flocculation flotation is a flotation technology that selectively flocculates fine-grained ilmenite by adding flocculants such as polyacrylamide to form flocs.
Agglomeration Flotation
Ilmenite agglomeration flotation is the flotation method in which the collector is adsorbed on the surface of ilmenite to make it hydrophobic, and the ore particle aggregates can be floating as a whole by the capillary attraction of the liquid bridge.
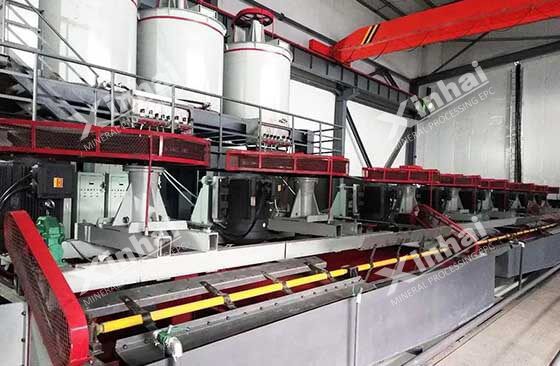
The above are five iron ore flotation methods. Some iron ore has the phenomenon of low grade, complex composition, fine embedded particle size, and uneven distribution. Only iron ore flotation is a more mature method for processing this type of (fine, micro-grained) iron ore.