With the rapid development of the global economy, the demand for iron ore from iron and steel enterprises increases rapidly, which further stimulates the development of the iron ore mineral processing industry. The subject of iron ore beneficiation in many kinds of iron ore is magnetite beneficiation. The common magnetite beneficiation processes mainly include a single magnetic separation process and low intensity magnetic separation-reverse flotation process.
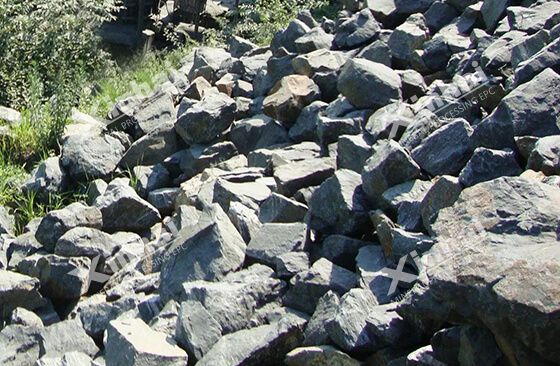
Use the table of contents below to navigate through the guide:
01Single magnetic separation process
The single magnetite ore is mainly sedimentary metamorphic magnetite. Most iron minerals in the ore are magnetite, which is mainly distributed with fine grains. The gangue minerals are mainly silicate minerals, such as quartz, hornblende, some of which contain more ferric silicate. This kind of magnetite is a kind of strong magnetic mineral with simple ore composition, the high grade and high recovery rate of iron concentrate can be obtained by the low-intensity magnetic separation method.
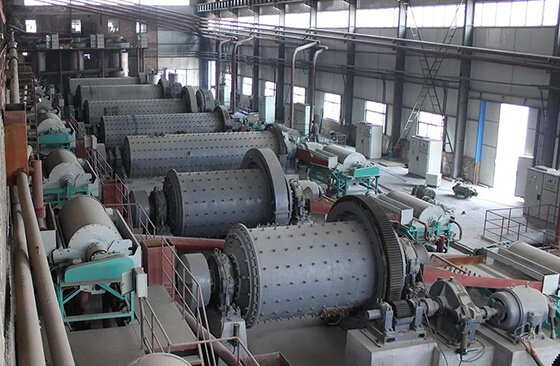
■ When the grinding size is greater than 0.2-0.3mm, the one-stage grinding-magnetic separation process is often used.
■ When the grinding size is less than 0.2-0.3mm, the two-stage grinding-magnetic separation process is adopted.
■ If the qualified tailings can be separated by the coarse grinding, the stage grinding-magnetic separation process is often adopted;
■ If the ore is mixed with a certain wall rock or there is a certain amount of monomer gangue minerals in all levels of crushing products, then a dry magnetic separator can be used for pre-separation before grinding.
In addition, for the low-grade lean magnetite ore, most magnetite concentrators often adopt the coarse-grained dry magnetic separation tailing discarding method, which can increase the processing capacity, selecting grade, and reduce the production cost through discarding a large number of tailings before the raw ore is sent to grinding.
For the ultra-lean magnetite ore with a grade below 20.00%, the grade difference between ore and surrounding rock is very small due to its low grade, whose beneficiation effect is not ideal by the dry magnetic separator.
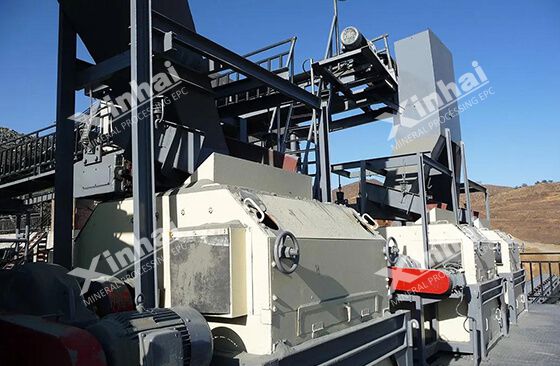
Therefore, the ultra-fine crushing and wet magnetic separation tailing discarding process can be adopted before grinding, that is, the ore is finely crushed to 5mm to 3mm below, and then wet magnetic separation tailing discarding is carried out with a permanent magnetic field magnetic separator, which can effectively improve the utilization rate of ultra-lean magnetite ore and the quality of final iron concentrate.
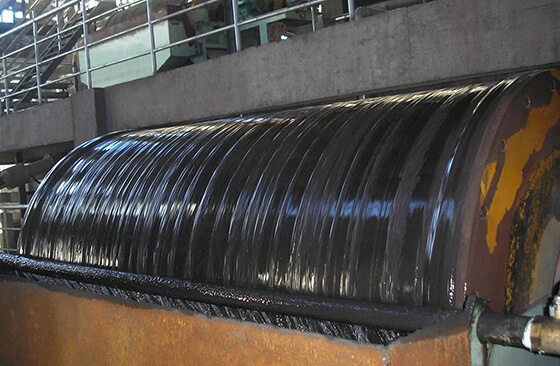
02Low intensity magnetic separation-reverse flotation process
The low intensity magnetic separate-reverse flotation process can be adopted when the magnetite ore contains silicate or carbonate minerals and is accompanied by cobalt pyrite, chalcopyrite and apatite, that is, iron can be recovered by a low-intensity magnetic separation process, and then sulfide or apatite can be recovered by reverse flotation process.
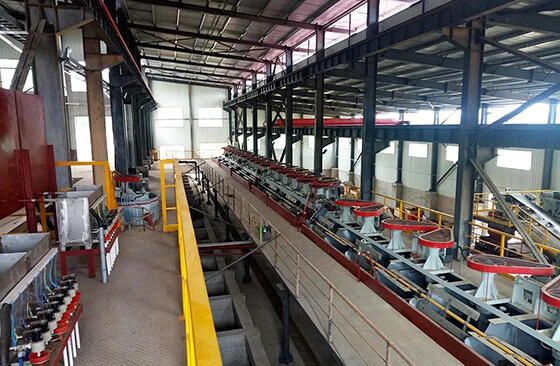
According to the different reagent systems, especially types of collectors, the low intensity magnetic separation-reverse flotation process can be divided into low intensity magnetic separation-cationic reverse flotation process and low intensity magnetic separation-anionic reverse flotation process.
Low intensity magnetic separation-cationic reverse flotation process
This method uses starch as the inhibitor of magnetite and amine agents (such as dodecylamine) as collectors. The required pulp temperature is low (above 25°C) and the pulp is neutral, which is especially suitable for treating magnetite with the high silicon content.
This magnetite beneficiation process has the advantages of a simple reagent system, low flotation temperature, suitable for field application, easy to operate, and strong adaptability to the change of process flow.
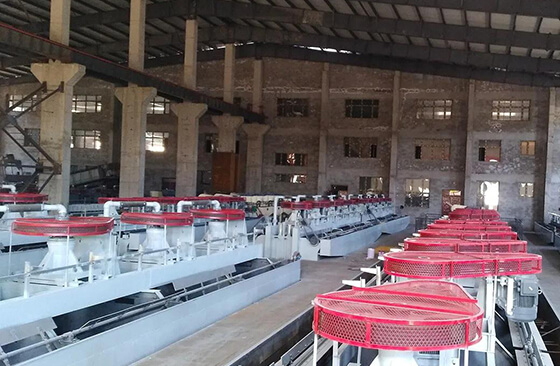
Low intensity magnetic separation-anionic reverse flotation process
The flotation foam is not sticky, the index is relatively stable, and this magnetite beneficiation process basically has no corrosion effect on rubber. However, there are many kinds of reagents used in anionic reverse flotation, and the flotation pulp temperature is required to be higher (above 30°C). The pulp is alkaline, which is conducive to pipeline transportation and direct filtration of concentrate, so acid treatment is needed before filtration.
Low intensity magnetic separation-anionic reverse flotation process is suitable for the magnetite ore with much iron-contained silicate minerals. Because the siliceous minerals are activated and the iron ore is inhibited selectively in the strong alkaline medium, the floatability difference between iron ore and siliceous mineral is bigger, which improves the flotation selectivity, thus obtaining the high-quality iron concentrate, and discarding the low-grade tailings. Besides, it also has good adaptability to the change of the floating material nature.
Low intensity magnetic separation-anionic reverse flotation process solves the problems of difficulty to improve the grade of iron ore concentrate and high silicon dioxide composition in iron concentrate, realizing the complementary advantages of the magnetite beneficiation process. Compared with the single magnetic separation process, the negative and cationic reverse flotation processes have a better flotation effect due to the large adjustment range and variety of reagents, which enhances the adaptability of the process flow and improves the quality.
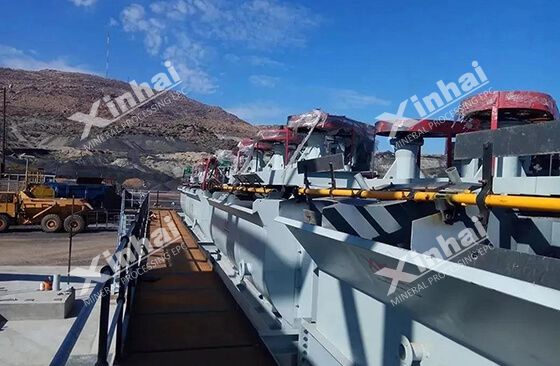
With the progressive fining in magnetite particle size, the negative impact of the magnetic poly group is increasingly obvious, and the magnetic minerals are mixed up with non-magnetic minerals. It is suggested to know the iron ore properties by mineral processing test, fully consider the plant condition, investment budget, thus customizing the magnetite beneficiation processes and equipment.