The flotation process is a more complicated beneficiation process. Flotation is normally undertaken in several stages to maximize the recovery of the target mineral or minerals and the concentration of those minerals in the concentrate while minimizing the energy input. The flotation separation process flow includes the one-stage flotation flow and stages flotation flow. So how do choose the flotation separation process flow?
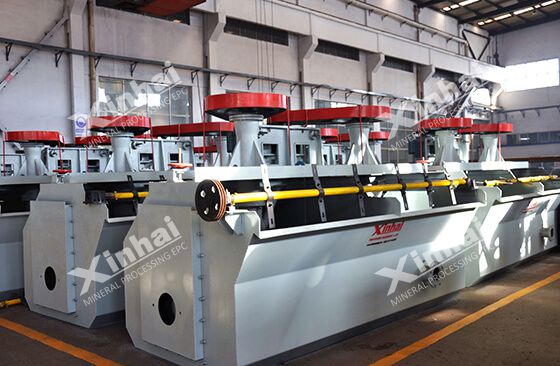
Use the table of contents below to navigate through the guide:
01One-Stage Flotation Separation Process Flow
The ore is directly grounded to the required particle size and then subjected to flotation to obtain the final product without re-grinding any product.
Application:
1. The useful mineral has uniform-grained dissemination and relatively coarse particle size, which is easy slimming.
For example, when the grinding particle size of heavy metal sulfide ore is For example, when the grinding particle size of heavy metal sulfide ore is 0.3mm, the qualified concentrate and discarded tailings can be obtained by using the one-stage flotation process to separate after coarse grinding.
2. The useful mineral has fine-grained dissemination and not uniform particle size, which is not easy slimming. For this kind of mineral, two consecutive grindings can be used before entering flotation, which is known as the one-stage flotation process.
For example, the particle size of some crystalline minerals needs to be grounded below 0.074mm to separate useful minerals. This kind of mineral has a fine and uniform particle size, which also meets the requirements of one-stage flotation.
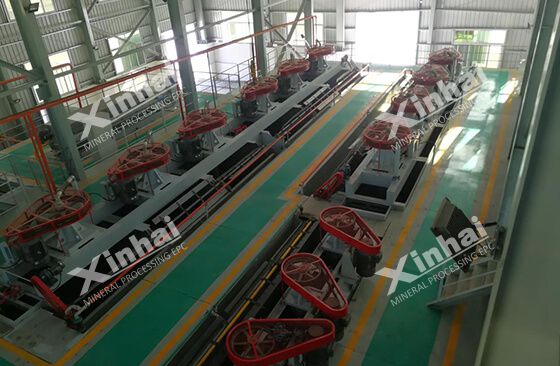
02Stages Flotation Separation Process Flow
The process of adding grinding operations after the flotation operation is the stages flotation process, which is mostly used to process ore with complex grain sizes or ore that is easy to mud. Stages flotation is divided into three situations: concentrate regrind, meddling regrind and tailings regrind.
1. Concentrate regrind
Application:
The ore contains two or more useful minerals, which are connected to each other, and the grain size of each useful mineral is finer, but their aggregates are thicker.
The first-stage grinding adopts coarse grinding to dissociate useful minerals and gangue; then the mixed concentrate obtained by flotation is regrounded and further dissociated; finally, the flotation operation is carried out to obtain useful mineral concentrates.
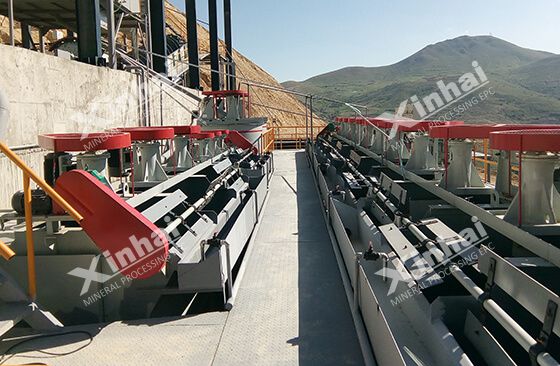
2. Meddlings regrind
Application:
The coarse and fine particles of useful minerals are not uniformly distributed, and the overall distribution is not uniform.
The first-stage grinding dissociates the coarse useful minerals and produces some gangue particles, which can be discarded as tailings. After one-stage flotation, some coarser concentrates, and some discarded tailings are obtained. The contiguous body enters the middle ore, which must be regrounded before fine-grained useful minerals can emerge.
3. Tailings regrind
Application:
The useful minerals are unevenly distributed in the ore, but the distribution in the tailings is uniform.
There are recoverable useful minerals in tailings.
The first-stage flotation obtains part of the concentrate. Then the tailings containing fine minerals are regrounded and re-floated to get useful minerals.
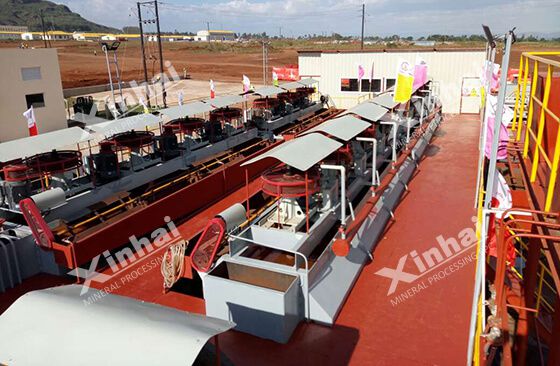
The choice of flotation Separation process flows mainly depends on the embedded characteristics of useful minerals. A reasonable flotation process is the main factor to reduce production costs. The mine owner can learn from the above contents in choosing the flotation Separation process flow, but in actual application, it is necessary to conduct ore beneficiation tests to determine the flotation process based on the analysis results.