It is one of the birthplaces of ancient humansAlso an African country with unique and amazing natural resourcesHereThere are wild animals in the background of KilimanjaroThere are also a variety of tribal cultureIt is the "land of cloves"With magnificent grassland, gobi and peakIt is also a mining countryInfrastructure production and resource mining & processing go hand in handThere is a broad space for cooperation in miningXinhai Mining also started its mining development in TanzaniaProject BackgroundWith the extension of mining depth, Tanzania M company found that the mineral properties of this project had changed compared with the previous ones. The single gravity separation process adopted by the original gravity separation plant was difficult to recover the gold ore effectively, and the technical indicators and economic benefits were not ideal, so Tanzania M company decided to build and reform the plant.
(The original gravity separation plant)In order to find a reasonable process, Tanzania M company had commissioned Russian and Chinese companies to carry out mineral processing tests. By comparing with several mineral processing enterprises, the customer sang high praise for the strict test, accurate data and detailed test report of Xinhai mine institute, and also gave the affirmation to Xinhai's strong brand strength, customized mineral processing EPC+M+O service, advanced and reliable equipment quality, and excellent service, finally reached the agreement with Xinhai Mining.
Project OverviewOre properties: The disseminated grain size of gold in the ore was very fine, the single gold is less than or equal to 30%, and the particle sizes of most gold were less than 13μm.
Processing capacity: 600TPD
Process flow: Two stages one closed circuit crushing and screening - two stages closed circuit grinding - CIL, desorption electrolysis - high-frequency furnace gold melting - tailings dry stacking process.
Main equipment: Plate feeder, jaw crusher, cone crusher, auto centering vibrating screen, grid ball mill, hydrocyclone, high efficient thickener, leaching agitation tank, desorption electrolysis system, high-frequency furnace, filter press, etc.
Xinhai Solution1. Crushing and screening stage:
The crushing stage adopted two stages a closed-circuit crushing process, the final particle size was less than or equal to 15mm. The raw ore was fed to the jaw crusher by the plate feeder, the crushing products were sent to the auto centering vibration screen by the belt conveyor for screening, the oversize products returned to the cone crusher, the products were sent to the auto centering vibration screen by the belt conveyor, and the undersize products were transported to the fine ore bin by the belt conveyor.
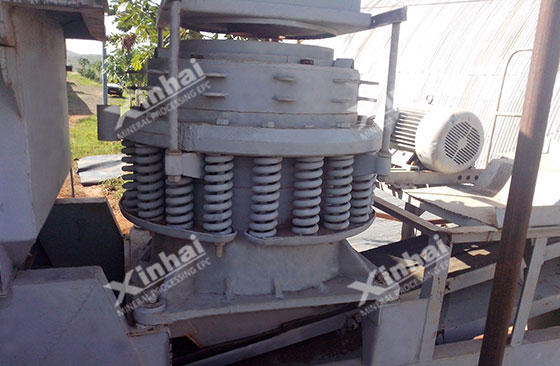
2. Grinding and classifying:
The grinding stage adopted two stages closed-circuit grinding process, and the grinding fineness (-200 mesh) accounted for 90%. The ore was transported to the grid ball mill for one stage grinding by the belt conveyor. The grinding concentration of the grid ball mill was 75-80%. The discharging pulp was sent to the drum screen at the end of the discharging port. The oversize coarse particles were fed by the belt feeder and returned to the grid ball mill for re-grinding (the cyclic load was about 80%). The undersize pulp was pumped to the hydrocyclone for classifying by the rubber pump, and the cyclone sand also returned to the grid ball mill for re-grinding (the cyclic load was about 130-150%), which formed a closed-circuit grinding. The cyclone overflow (f -200 mesh particle sizes were about 60% and the solid weight concentration was about 40%) entered into the second closed-circuit grinding stage.
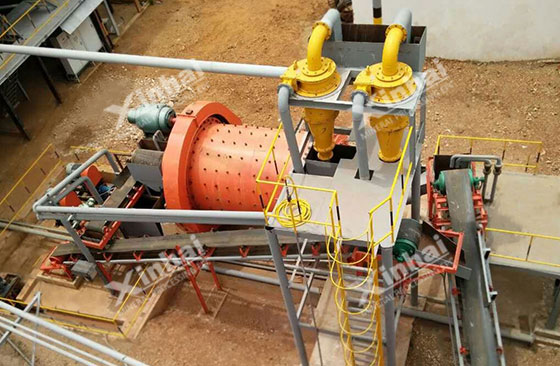
The second grinding stage was composed of three series, so the cyclone overflow in the first stage closed-circuit grinding was divided into three channels of slurry by the slurry distributor. Each slurry was pumped o the hydrocyclone for classifying by the rubber pump, and the sediment entered into the overflow ball mill for fine grinding (the grinding concentration was about 70-75%). The fine grinding products and slurry before classifying are pumped into the hydrocyclone, which formed the second closed-circuit grinding cycle (the circulating load was about 225%). Three series of cyclones overflow (-200 mesh particle sizes were approximately 90%, and the solid weight concentration was approximately 20-25%) entered into the next stage.
3. Cyanide leaching and carbon absorption stage:
After two stages grinding, the pulp concentration of qualified products was about 20-25%, which cannot reach the solid weight concentration required (40%) by leaching. Therefore, the thickening operation was required to improve pulp concentration before leaching. The second stage of hydrocyclone overflows entered into the linear vibrating screen to remove wood chips. Then, the slurry flowed to the high efficient thickener for increasing the slurry concentration to 40%. After the adsorption column absorbed the gold, the water returned to the process for recycling, and the underflow of thickener entered the cyanide leaching stage.
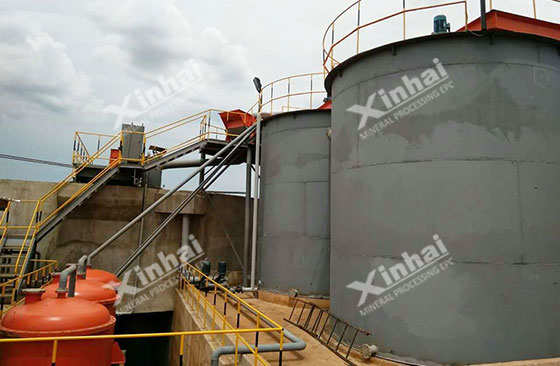
The thickener underflow (-200 mesh particle sizes accounted for 90% and the concentration was 40%) was pumped to the No.1 leaching tank to the No.7 leaching tank successively through the rubber pump. 10% sodium cyanide solution and lime solution flowed into 1#, 2#, 4# and 6# leaching tanks, making the CN- reach 300-500PPM and the CaO content reaches 100-200PPM. The activated carbon was added from the 7# tank to the 1# tank in turn. There was a carbon screen installed at the outlet of each leaching tank to prevent the activated carbon in each leaching tank from flowing into the next leaching tank. When the gold-loaded activated carbon was lifted from the 1 # leaching tank, the linear vibration screen was used to screen out the carbon, and the pulp returned to the 1 # leaching tank. Finally, the leaching rate of gold reached 91.64% and the adsorption rate of carbon reached 99.00%.
4. Desorption electrolysis stage:
This stage adopted high temperature and high-pressure cyanid-free desorption electrolysis system, which was featured with high efficiency, fast speed, low consumption, non-toxic (NaCN) and automatic control. The working temperature of the system was about 150 degrees celsius and the working pressure was about 5 bar. The gold was desorbed within only 12 to 15 hours.
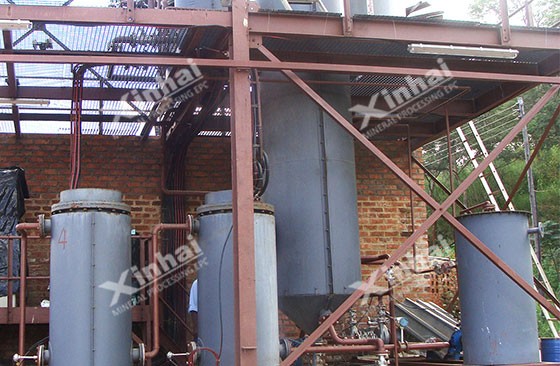
5. Smelting stage:
The gold slime produced by desorption electrolysis stage was treated by pickling and then fed into high-frequency smelting furnace for smelting. Finally, the gold ingot was obtained.
6. Tailings dry stacking stage:
The cyanidation leached tailings were screened by the safe screen for preventing the loss of gold and carbon, and then entered into the buffer tank, then were driven into the press filter by the alloy pump for pressure and dehydrate. The tailings filter cake was sent out by the belt conveyor, and the filter liquor returned for recycling. The moisture content of the tailings filter cake was only 20%, which was stacked in the tailings pond.
Projects Highlights1. Tailored solution and reasonable layout
◆ On the basis of the original gravity separation plant, Xinhai Mining appropriately added new equipment and technology, maximized the use of the original plant, equipment and foundation;
◆ The scientific and reasonable plant design ensured the smooth flow of the whole plant, the new and old equipment ran normally, which not only achieved the expected recovery rate, but also saved the investment cost.
2. Advanced process and realizable equipment
◆ Two stages grinding operation used the slurry pump, hydrocyclone instead of the traditional spiral classifier, which had the advantages of high efficiency, less power consumption and low investment;
◆ The thickening operation before leaching adopted high efficient thickener. Reducing the diameter of the thickener greatly saved the equipment cost. At the same time, adding some flocculant significantly reduced the settling area and time of the thickener;
◆ Adopted the high temperature and high-pressure cyanid-free desorption electrolysis system, efficient, fast, low consumption and non-toxic.
3. Green and environmental protection
Generally, the cyanidation tailings were easy to pollute the atmosphere due to small particle size. And residual cyanide roots can cause water pollution if they entered into the environment. The normal tailings of this concentrator had the small particle size, but the water content was only 20%, so they cannot fly. Moreover, the normal tailings of this concentrator contained very little cyanide, so it was very unlikely to enter the environmental water.
Customer Feedback"Today, Xinhai Mining has become a well-known mineral processing brand in Tanzania and even the whole of Africa. Many mineral processing plants in Tanzania choose to cooperate with Xinhai Mining. Its one-stop mineral processing EPC+M+O service really considers for customers, and starts from the actual conditions, the process flow was scientific and reasonable, the equipment ran stably, so the plant benefit was ideal. This time, we selected Xinhai Mining with both strength and reputation, and the fact proved that our choice is right!"
(Site of Tanzania 600tpd gold ore processing plant)Though vast oceans keep China and Tanzania far apart, the friendship between our peoples has a long history and, having been tested by times, is strong and vigorous. Six hundred years ago, the ancient maritime silk road served as a bridge for exchanges between China and Tanzania. Six hundred years later, the 21st-century maritime silk road created by "One Belt And One Road" Initiative has also brought new vitality to china-Tanzania cooperation. In Africa, Xinhai Mining has undertaken hundreds of mineral processing EPC+M+O projects in Tanzania, Zimbabwe, Sudan, Nigeria and other African countries, and has been effectively promoting the development of the African mining industry. In the future, Xinhai Mining will also actively respond to the "One Belt And One Road" Initiative, lead Tanzania and even the whole African mining industry to a new height.